Fast, agile and efficently managed maintenance
- Hannah Allen
- May 15, 2023
- 3 min read
BY DARREN LEWIS | 15-5-23
Maintenance operations are an integral part of any Solar Farm operation. The ability to respond quickly and efficiently to incidents is crucial in minimising downtime, reducing costs, and ensuring optimal performance. In this blog post, we will explore the benefits of SGU's maintenance model, highlighting the importance of data models in predicting spare part requirements and maintaining optimal stock levels. By leveraging data-driven approaches, we can enhance our incident response time while simultaneously achieving cost-effectiveness.
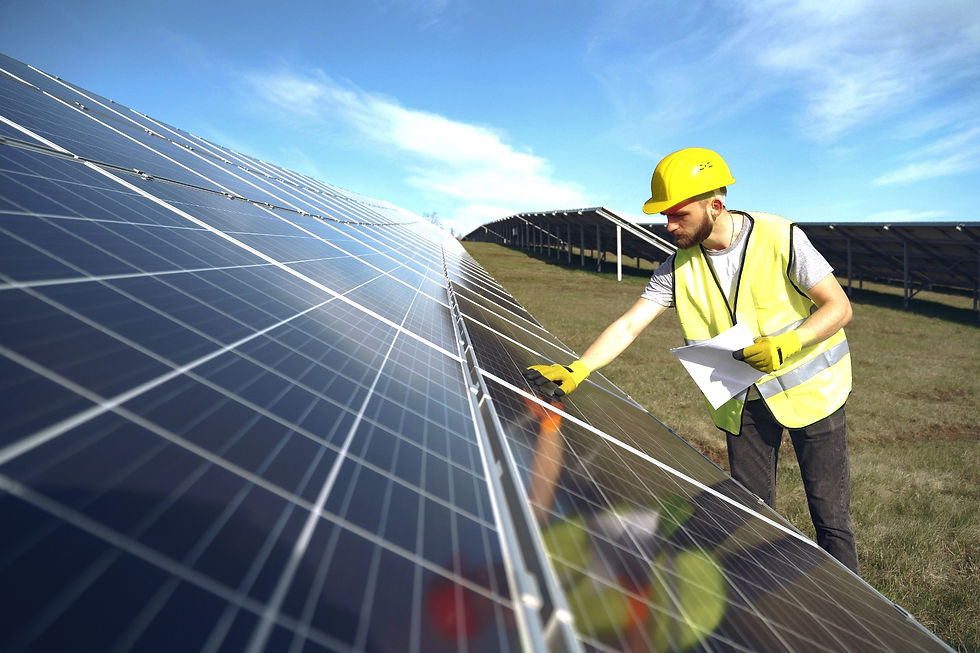
Predictive Maintenance and Spare Part Management:
Gone are the days when maintenance was solely reactive, waiting for equipment failures to occur before addressing them. Today, we embrace predictive maintenance strategies to anticipate and prevent potential issues before they disrupt operations. A key component of predictive maintenance is the ability to accurately forecast the need for spare parts.
Data models play a crucial role in predicting spare part requirements. By analysing historical data, monitoring equipment health, and considering various factors such as usage patterns, environmental conditions, and maintenance schedules, our models can estimate the probability of component failure. This proactive approach enables us to maintain optimal stock levels of spare parts, ensuring they are readily available when needed.
Core In-House Team and Contractor Support:
To efficiently manage maintenance operations, we rely on our core in-house team of skilled engineers and contractor support. Ensuring that the right expertise is available when required. The in-house team brings deep knowledge of SGU's infrastructure, processes, and systems, while contractors offer specialised skills and additional resources.
By leveraging the expertise of both teams, we enhance our maintenance capabilities. The core in-house team serves as the backbone, providing continuity, and possessing a comprehensive understanding of the equipment and maintenance history. Contractors bring fresh perspectives, specialized knowledge, and additional manpower, enabling faster incident response and resolution.

Optimal Stock Levels and Cost-Effectiveness:
Maintaining optimal stock levels of spare parts is a delicate balance. On one hand, excess inventory ties up capital and increases storage costs. On the other hand, insufficient stock levels can lead to delays in incident resolution and prolonged downtime. Our data models provide the necessary insights to strike this balance effectively.
By analysing historical data and considering factors such as equipment failure rates, lead times for spare part procurement, and costs associated with downtime, we can determine the optimal stock levels for each component. This data-driven approach helps minimise the risk of stockouts and excess inventory, ultimately reducing costs and ensuring efficient maintenance operations.
Fast Incident Response Time:
The combination of predictive maintenance strategies, a well-managed spare part inventory, and a skilled maintenance team enables us to achieve fast incident response times. Predictive analytics helps identify potential issues in advance, allowing maintenance teams to proactively address them before they cause significant disruptions.
Having spare parts readily available at optimal stock levels further accelerates incident response time. When a failure occurs, the maintenance team can quickly access the required components, reducing downtime and minimising the impact on operations. This swift response not only enhances operational efficiency but also contributes to increased customer satisfaction and minimised revenue loss.
Fast, agile, and efficiently managed maintenance operations are essential for SGU to thrive in a competitive landscape. By leveraging data models to predict spare part requirements and maintaining optimal stock levels, we can enhance our incident response time, achieve cost-effectiveness, and minimise downtime. A core in-house team of engineers, supported by contractors, complements the data-driven approach by providing expertise, scalability, and flexibility. Ultimately, the integration of these strategies empowers us to proactively address maintenance issues, improve operational efficiency, and deliver superior customer experiences.
If you'd like to find out more about optimising your solar PV yield through effective O&M - then we're ready to talk.

DARREN LEWIS
Managing Director
Connect with me on LinkedIn
Darren is responsible for all operational aspects of our service provision. This includes, site survey, workflow, training and the assessment, onboarding and development of our contract partners. With 20 Years in Electrical Installation and PV, there is huge amount of industry change that he has been an integral part of and his approach is that every day brings a new opportunity for further process improvement.
Our Story
We have a proven O&M solution that has been supporting the industry as a hidden partner for over 20 years, combined with a the revolutionary workflow that we have developed and an agile UK wide team of O&M Engineers.
We'd love to tell you more.